NPMpc
1,2 drives, 12-100v, up to 13.3/40A
100V/40A, PCB Mounted NanoPWMTM 1 / 2 Axis EtherCATTM Drive Module
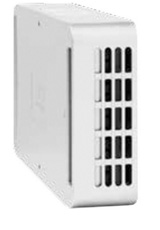
Powerful and Compact
- Two drives per module for Gantry control
- Voltage: 12Vdc – 100Vdc
- Current: Up to 13.3A / 40A (cont./peak)
- PCB mounted to fit connectivity needs
Better Than Linear Drives
- Lower heat dissipation
- Better reliability
- Significantly smaller
- Simpler supply requirements
- Digitally controlled
- Easy setup
Uncompromising speed and resolution
- Up to 4 Analog Sin-Cos 1Vptp encoders with frequency
up to 10MHz
- Encoder multiplication of 4 to 65,536
- Automatic encoder compensation and error detection
- Dual feedback support
- Two squared Sin-Cos outputs
- Position feed-forward for active vibration isolation
systems
- Relays control outputs for dynamic braking
- Safe Torque Off (STO)
Smart Motion related I/O
- 4 encoder registration MARK inputs
- 2 Position Event Generators
- 2 motor brake / Relay outputs
- 4 analog inputs, 12 bit resolution, ±10V
- 4 analog outputs, 16 bit resolution, ±10V
The NPMPC Is a line of the most advanced PWM servo drives available today. |
|
It is specifically designed to address the most demanding applications with regards to move and settle times,
standstill jitter, and velocity smoothness, such as wafer metrology and inspection, FPD inspection, and ultra-precision
machining for processing of optical components. The NPMPC is based on the ACS proprietary technology
that exceeds stand still jitter and tracking error performance that until now has been achieved only with linear drives,
with reduced cost of ownership.
With the optional combination of a 10MHz laser encoder interface and the powerful algorithm, demanding
sub-nanometer resolution positioning systems can achieve ultimate throughput and accuracy with minimal sensitivity
to disturbances and stage to stage manufacturing differences.
The NPMPC is designed to be mounted on a custom carrier board. It enables customizing connectors, I/O configuration,
STO and other safety function implementation.
For prototype testing and carrier board design reference it is recommended to use the NPMPM.
The NPMPC is a slave that runs under any ACS EtherCAT masters.
A comprehensive set of software support tools are provided for module configuration, setup and tuning.
CE, UL (Pending)
EtherCAT® is registered trademark and patented technology, licensed by Beckhoff Automation GmbH, Germany
Specifications
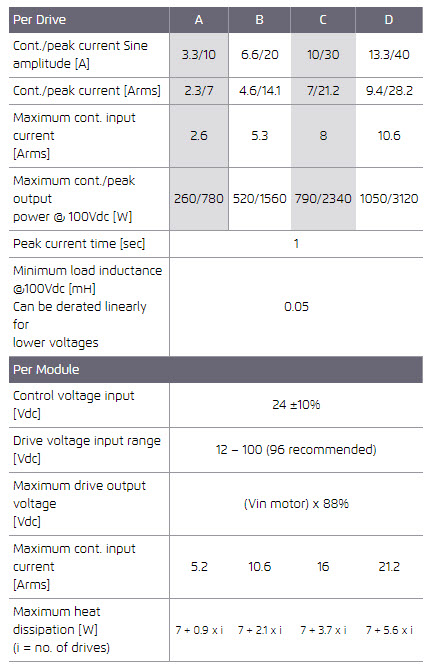
Drives
Type: digital current control with field oriented control and space vector
modulation.
Current ripple frequency: 40 kHz.
Current loop sampling rate: 20 kHz.
Programmable Current loop bandwidth: up to 4kHz, will vary with tuning & load parameters.
Commutation type: sinusoidal. Initialization with or without hall sensors.
Switching method: advanced unipolar PWM.
Protection: Over and under voltage, Over current, Over-temperature, Phase to phase and phase to ground short (short circuit on one of the motor phases might damage the drive).
Supplies
The module is fed by two power sources. A motor supply and a 24Vdc control
supply. During emergency conditions there is no need to remove the 24Vdc
control supply.
Motor Drive Supply:
Range: 12Vdc to 100Vdc,
Recommended: 12Vdc - 96Vdc.
Current rating should be calculated based on actual load.
If regen resistor is required, it should be added in parallel to motor supply
with 102V activation.
Control Supply:
Range: 24Vdc ± 10%.
Maximum input current / power:
0.9A @ 21.6V/ 20W without motor brakes.
With two motor brakes: 1.9A @ 21.6Vdc/ 42W.
Protection: reverse polarity. A 3A external fuse must be used.
Motor Type
Two- and three-phase permanent magnet synchronous (DC brushless/AC servo), DC brush, Voice coil, Two- and three-phase stepper (micro-stepping open or closed loop).
Feedback
Types: Incremental digital encoders (AqB), Hall inputs, analog Sin-Cos
(optional), absolute encoders (optional).
Incremental Digital Encoder: Two per axis. A&B, I and Clk/Dir,
Type: Differential RS-422. Max. rate: 50M quad counts/sec.
Protection: Encoder error, not connected.
Sin-Cos Analog Encoder: Up to two per axis.
Type: 1Vptp, differential.
Programmable multiplication factor: x4 to x65,536.
Maximum frequency: 500kHz or 10MHz.
Maximum acceleration with Sin-Cos encoder: 108 sine periods/second2.
Squared Sin-Cos output: Two, differential RS422.
Absolute Encoder (optional): Up to two. EnDat 2.1 (digital)/ 2.2, Smart ABS,
Panasonic, BiSS-A/B/C, SSI, Sanyo ABS.
Hall inputs: A set of three per axis.
Type: single-ended, 5V, source, open cathode. Input current: <7mA.
Feedback supplies: For all digital feedback devices: 5V, 0.5A.
For all analog feedback devices: 5V, 1.5A.
Digital I/O
For different I/O configurations see ordering options.
Inputs
Safety: Left & right limit inputs per axis.
Type: 24V/ source (default), single ended, opto-isolated. Input current 4-14mA.
Registration Mark: (High Speed Position Capture): Four, 24V±20%,
opto-isolated, two terminals. Input current 4-14mA.
All dedicated inputs can be used as general purpose inputs.
Outputs
Motor Mechanical Brake: Two, 24V/source (default), single ended,
opto-isolated, 0.1A.
PEG (Position Event Generator): Two, Pulse or State, Differential, RS422.
Pulse width: 26nSec to 1.75mSec. Maximum rate: 10MHz.
All dedicated outputs can be used as general purpose outputs.
Analog I/O
Analog Inputs: Four, ±10V, differential, 12 bit resolution.
Max. input frequency: 1 kHz. Offset: <30 mV.
Analog Outputs: Four, ±10V, differential, 16 bit resolution.
Offset: ±50mV, Bandwidth: 5 kHz. Max. output load: 10KΩ, Noise/Ripple: <40mV.
STO (Safe Torque Off)
Supports STO design to be implemented on the carrier board.
EtherCAT Communication
In and Out.
Environment
Operating range: 0 to + 40°C.
Storage and transportation range: -25 to +60°C.
Humidity (operating range): 5% to 90% non-condensing.
Dimensions
155 x 85 x 30 mm3.
Weight
360 gr.
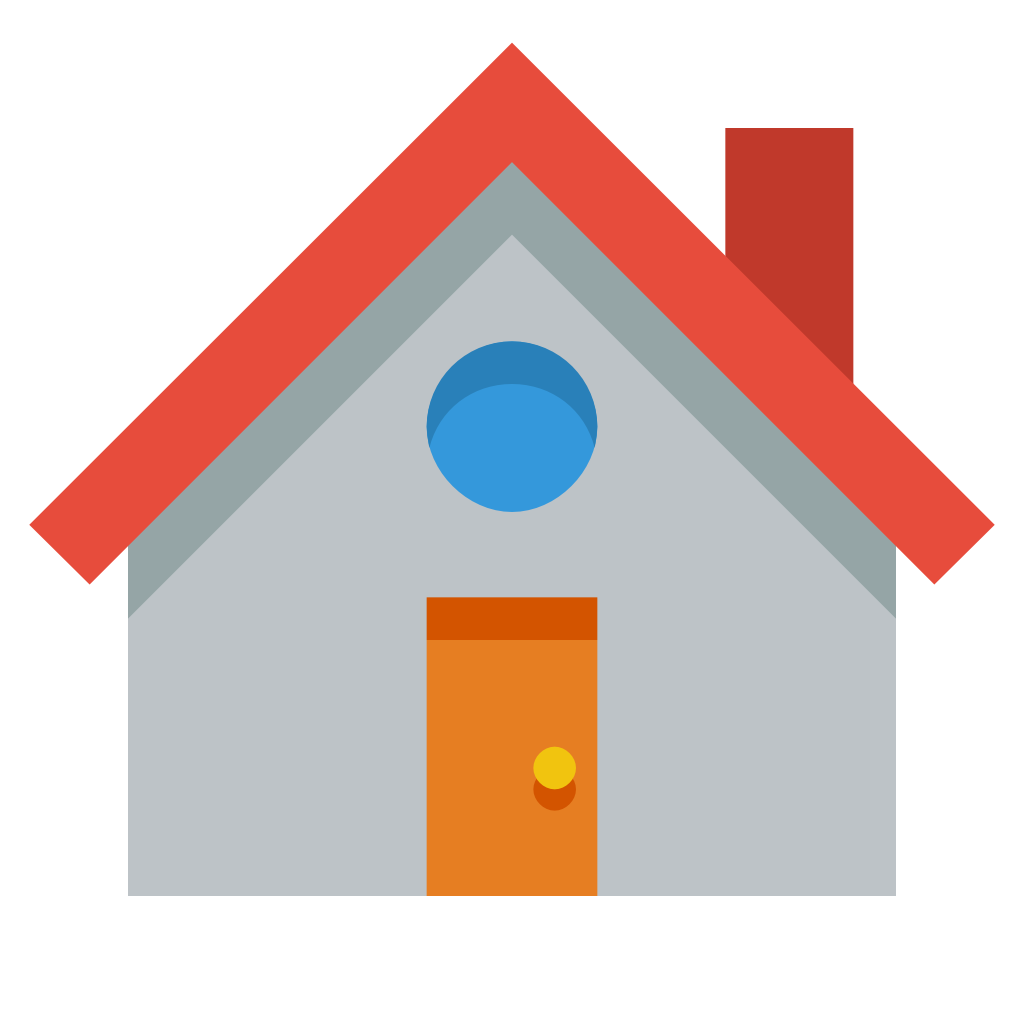
|